Description of the Process
The plastic recycling process is a critical component in the effort to reduce plastic waste and promote sustainable resource management. This process involves a specialized line that converts used plastic bottles, caps and labels into valuable recycled materials.
The line begins with the collection of plastic bundles, which are meticulously processed through various stages such as bale opening, ballistic separation, metal and aluminium separation, pre-washing, and label removal. These initial steps are crucial for eliminating contaminants and preparing the plastic for further processing.
Next, the plastic material undergoes optical sorting, crushing, friction washing, rinsing, drying, and colour sorting. These stages further clean and refine the plastic material, making it ready for conversion into flakes.
The equipment and processes are grouped into three main categories: Separation, Crushing and Washing-Drying and Packaging. Each group contains specific machines that work together to ensure efficient recycling.
This advanced recycling system not only helps reduce plastic waste but also produces high-quality recycled plastic materials, contributing to a more sustainable environment. The project aims to recycle PET, HDPE and PP waste while minimizing the energy consumption needed to produce plastic products from virgin materials, thereby reducing greenhouse gas emissions (GHGs). Compared to traditional plastic production methods, this project is more energy-efficient, directly lowering GHG emissions and aiding in the fight against climate change.
Plastic bundles are transported along the conveyor belt, which connects various processing stages given in Figure 1:
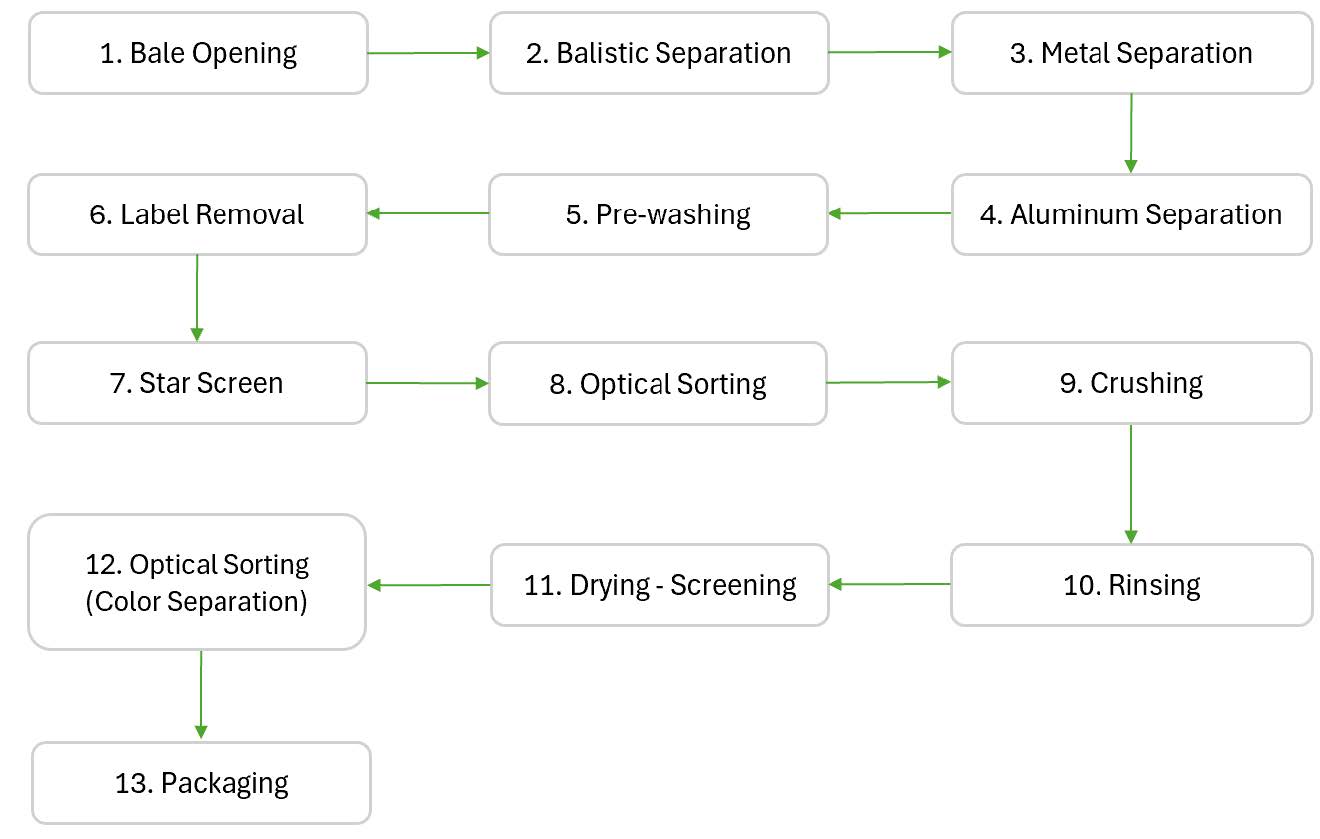
Figure 1. Process Description Scheme of Project Activity
The process for the recycling of plastic bottles involves multiple stages, each with specific equipment designed to sort, clean, and process the materials:
- Bale Opening: The process begins with the Bale Opener, where compacted plastic bales are broken apart, allowing the bottles to be fed into the system individually.
- Ballistic Separation: The Ballistic Separator differentiates between two-dimensional materials like labels and films from three-dimensional objects such as plastic bottles and aluminum cans. Heavier, three-dimensional materials move on to the next stage, while lighter, two-dimensional materials are separated out.
- Metal Separation: The Metal Separator utilizes magnets to remove ferrous metals mixed with the plastic bottles.
- Aluminum Separation: The Aluminum Separator identifies and removes aluminum cans and other non-ferrous metals from the stream using a high-frequency magnetic field.
- Pre-washing: The bottles are subjected to Pre-washing, which involves spraying water on the bottles as they rotate in a drum. This step helps to remove dirt, soil, and other contaminants from the surfaces of the bottles.
- Label Removal: In the Label Removal stage, the bottles undergo further cleaning to strip away any attached labels. This is crucial to ensure that only clean plastic enters the next processing stages.
- Star Screen: Bottles are spread out on the Star Screen to ensure an even distribution on the conveyor for the next stages.
- Optical Sorting: At the Optical Sorting stage, high-speed optical sensors classify bottles based on their color or material type, using laser technology to direct them to the appropriate output chute.
- Crushing: The bottles are then Crushed into smaller flakes or “cracklings,” making them easier to clean and process in subsequent stages.
- Rinsing: The flakes undergo Rinsing to remove any remaining contaminants, ensuring a higher purity of the plastic material.
- Drying – Screening: The crushed material is Dried and Screened to remove small debris and prepare the plastic flakes for further processing.
- Optical Sorting (Color Separation): A second Optical Sorting stage further separates the plastic flakes by color, ensuring that the final product is uniform.
- Packaging: Finally, the plastic flakes are Packaged for sale or further processing, completing the recycling process.

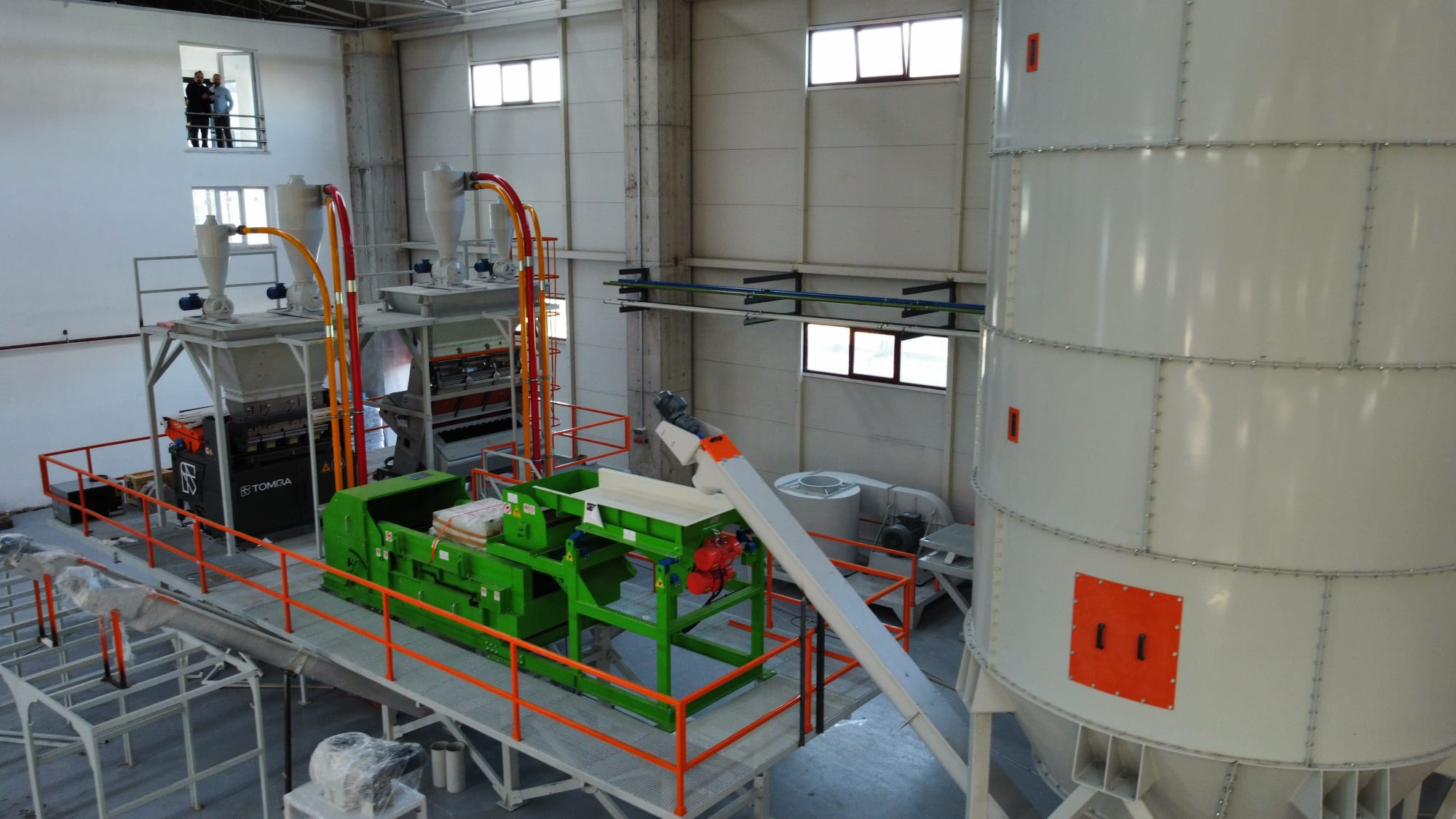
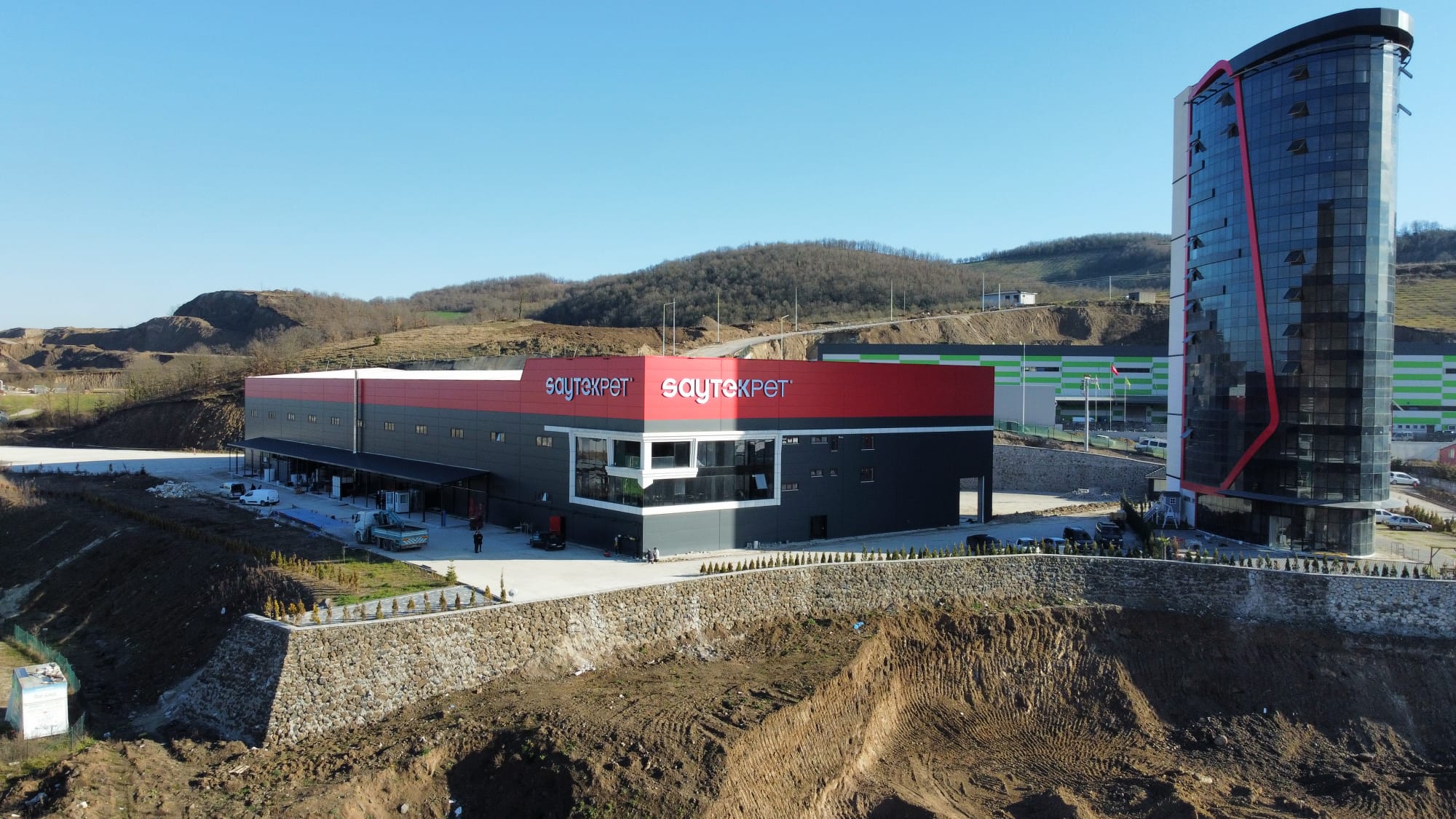